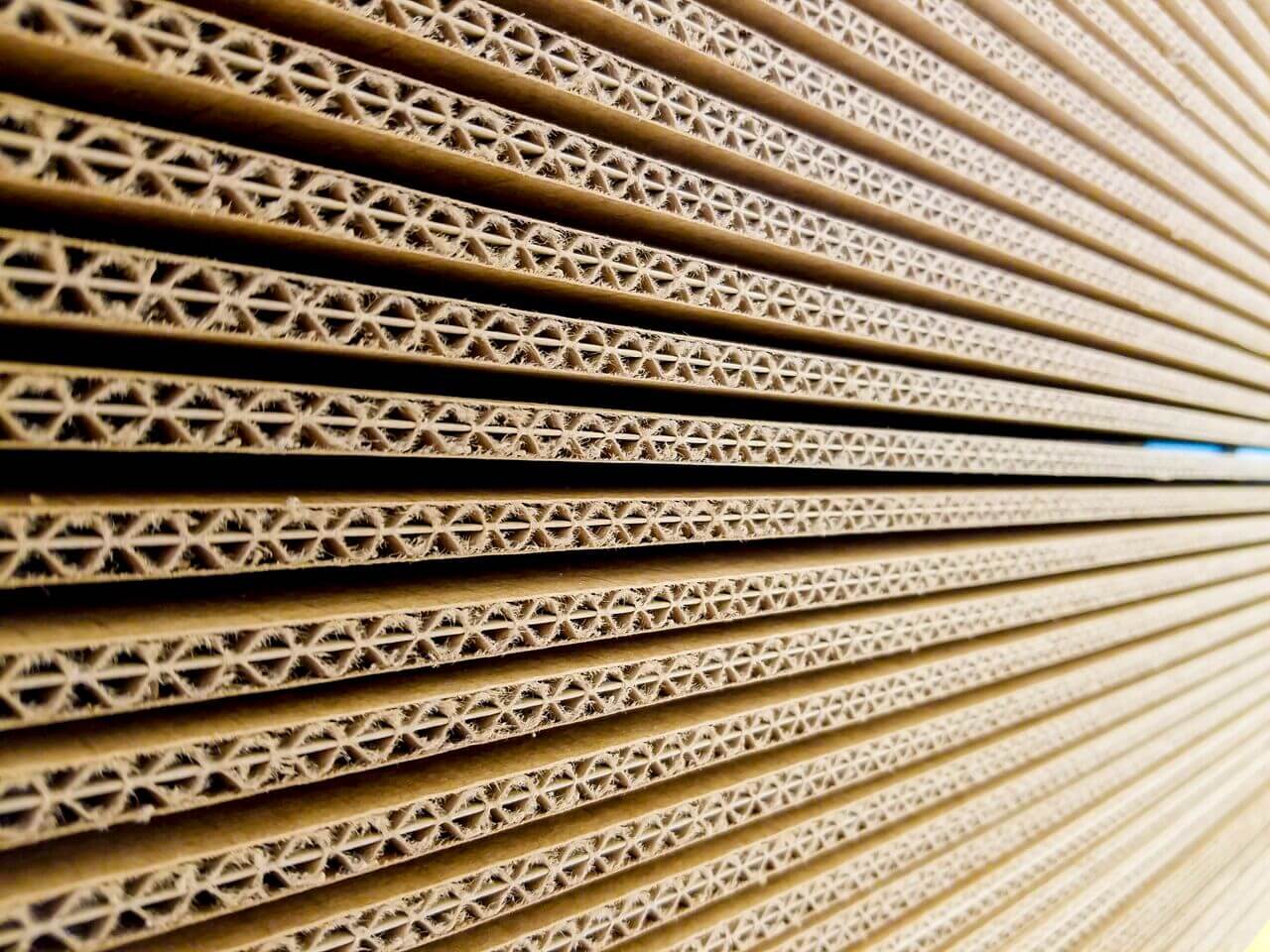
Supply Chain Optimization
$1.1 Million in Freight Savings Alone
The Challenge:
We faced two challenges in optimizing package design for a large automotive interior component supplier. They needed to eliminate damage and find packaging cost savings for a part delivered to and used in their assemblies.
The Solution:
Our engineers redesigned and right-sized the packaging to better protect the part. We increased the material strength and glued in partitions for easy pack-out and added support so that cartons could be used as WIP packaging, and shipped to customers in the same cartons.
We also reoriented the placement and loading of the part, making room for two parts per cell instead of one.
The Results:
The component supplier now delivers a quality part, and has robust packaging for use throughout the supply chain. Savings include:
- Reduction in plant packaging warehousing costs: 50%
- Reduction in box setup labor costs: 50%
- Reduction in material handling costs: 50%
- Reduction in corrugated breakdown/waste removal costs: 50%
- Reduction in plant floor space: 50%
- Freight savings: $1,152,000
- Carbon footprint reduction: 300 fewer trucks on the road
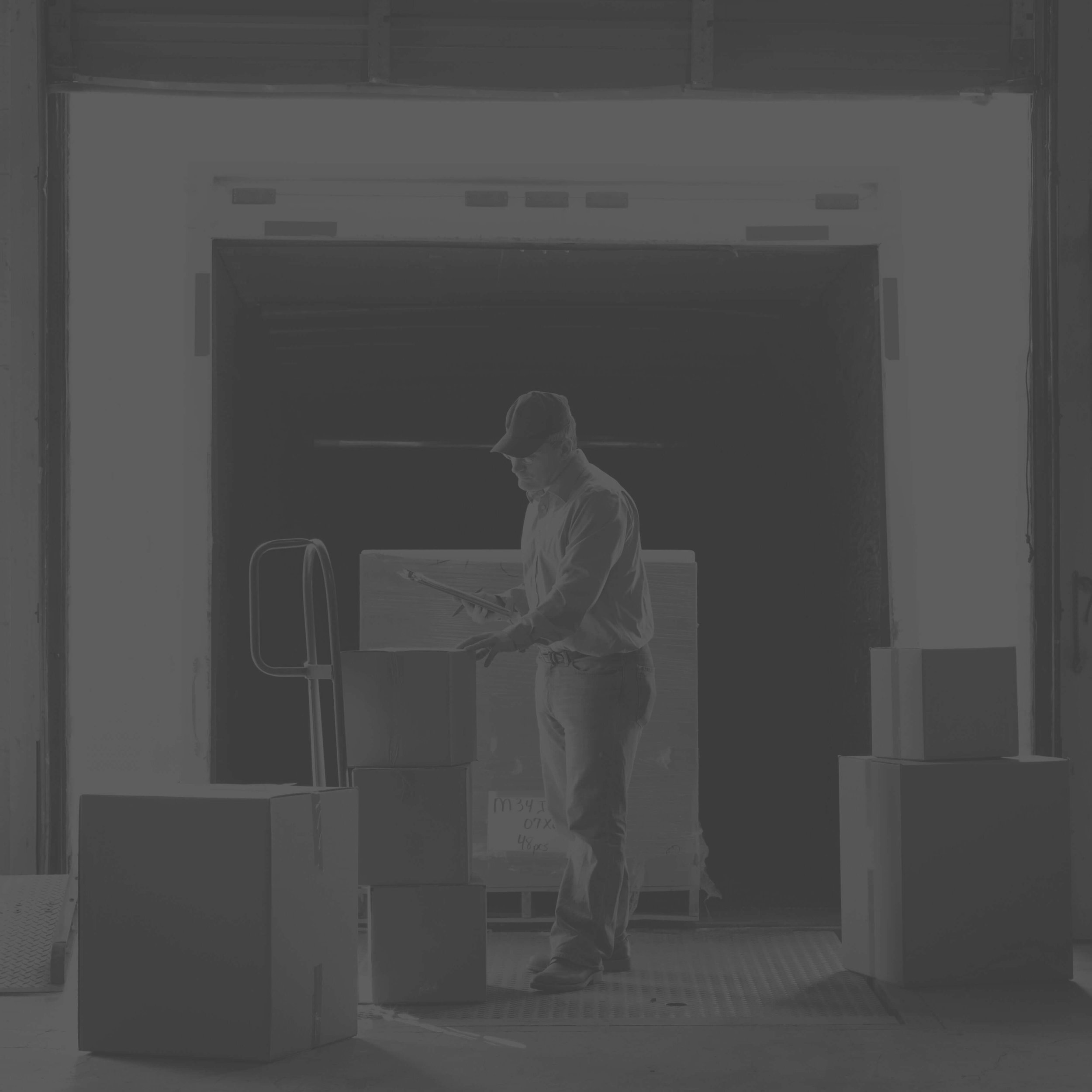
Shifting From Expendable to Returnable
Nearly $3 Million in Savings Over a Four-Year Program
The Challenge:
We were asked to evaluate an OEM’s finished goods packaging and determine if it could be reused at least five times before replacing. The packages were returnable and the internal dunnage was one-way.
We were also asked to develop a returnable option for providing cost savings spread out over a shortened ROI program of four years.
The Solution:
We performed trials to determine how many times their expendable one-way packaging could move between the supplier and the assembly plant. It turned out to be fully expendable, only protecting parts for a single delivery.
The next step was to make a business case for returnable dunnage that could fit in existing containers. We redesigned their foam pads using heavy-duty, plastic-corrugated sheets. Dense foam logs within the sheets’ die cavities could hold the part, and prevent the part seal from contacting the dunnage that was deforming the parts.
The Results:
- Annual savings: $745,442
- Four-year program savings: $2,981,768
- ROI: .77, well under the one-year target
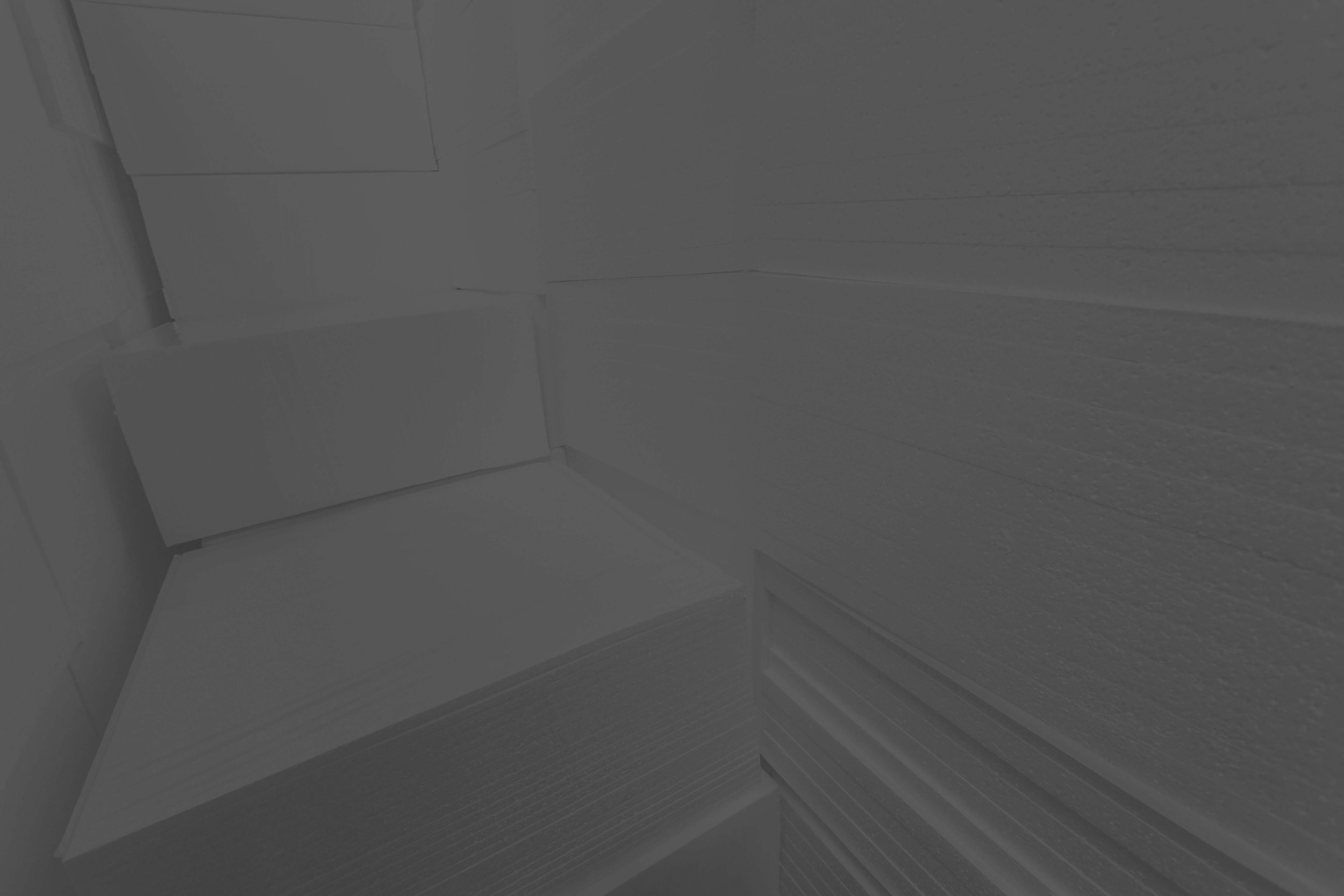
Materials Selection for Cost Optimization
Parts Damage Reduced From 11% to 0%
The Challenge:
A supplier of high-gloss painted parts was receiving complaints about marks on their parts from shipping. We were asked to redesign their returnable packaging with materials that could protect the part from scratches and allow it to cure safely in the packaging.
The Solution:
We performed trials with a number of fabric materials typically used for Class A parts. No parts survived intact — all materials caused a slight scratching or smudging. Since no existing material served our needs, we developed a material of our own.
The Results:
- Parts damage reduction: from 11% (330 damaged parts per week) to 0%
- New material cost reduction: 25%
- Dunnage assembly savings: $150,000 annually
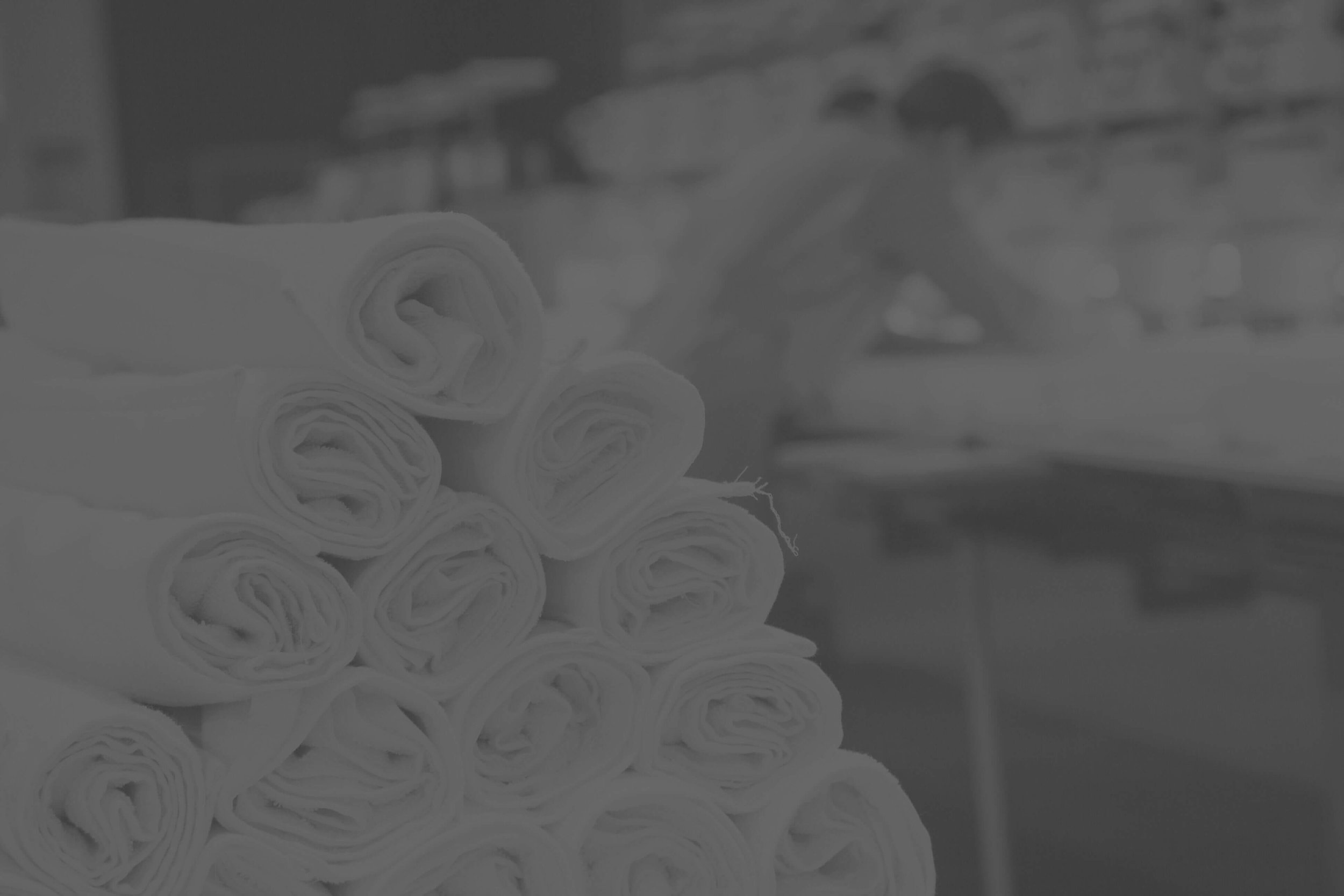